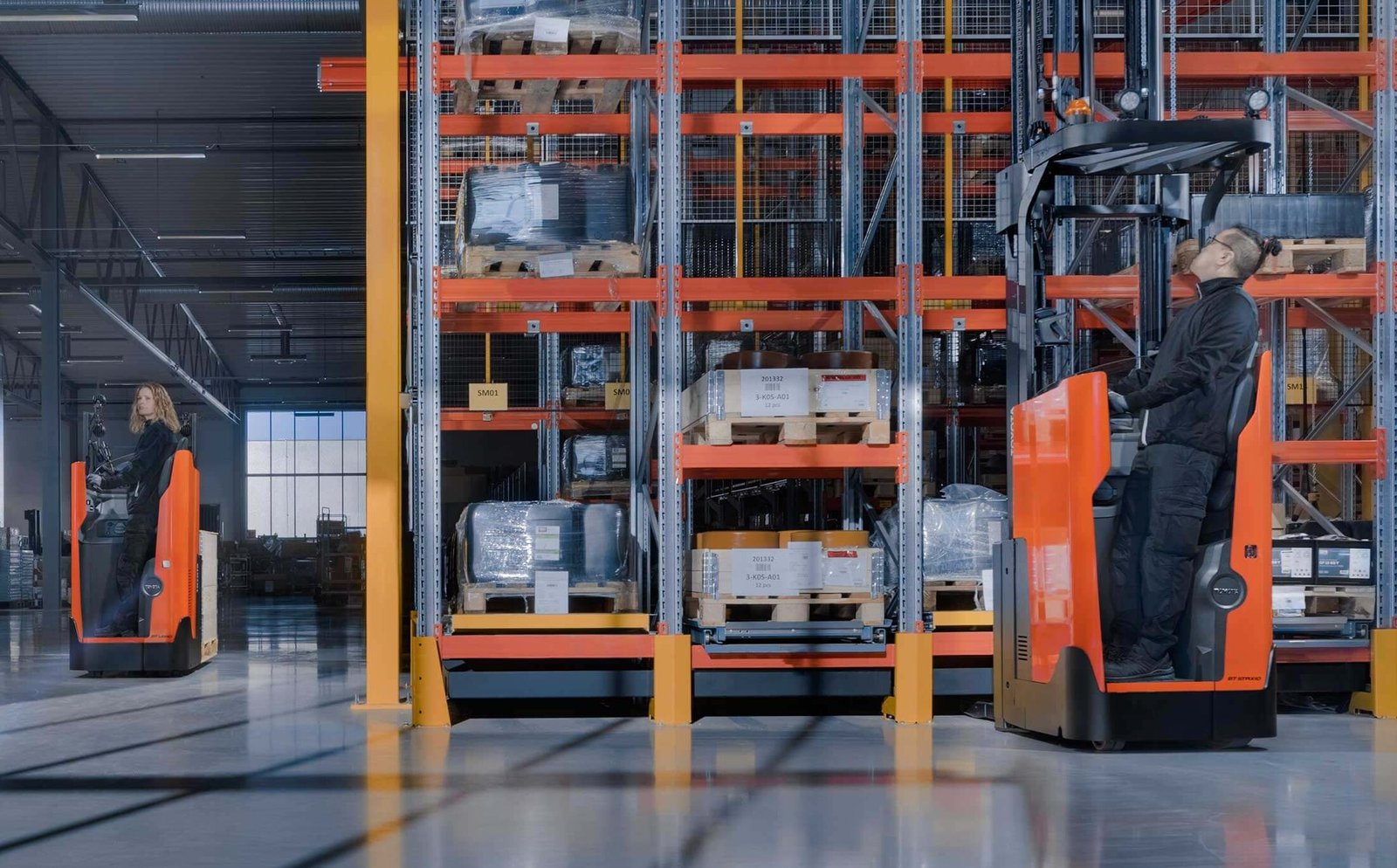
17 Warehouse Efficiency Improvement Tips: What Can It do for Your Productivity?
To elevate your warehouse’s performance, you need to embrace efficient practices and innovative solutions. Start by optimising your layout, reducing travel time, and investing in a robust Warehouse Management System (WMS).
Employee training, open communication, and leveraging omnichannel fulfilment will enhance customer satisfaction and streamline processes. Let’s dive into these strategies to help you transform your warehouse into a top performer.
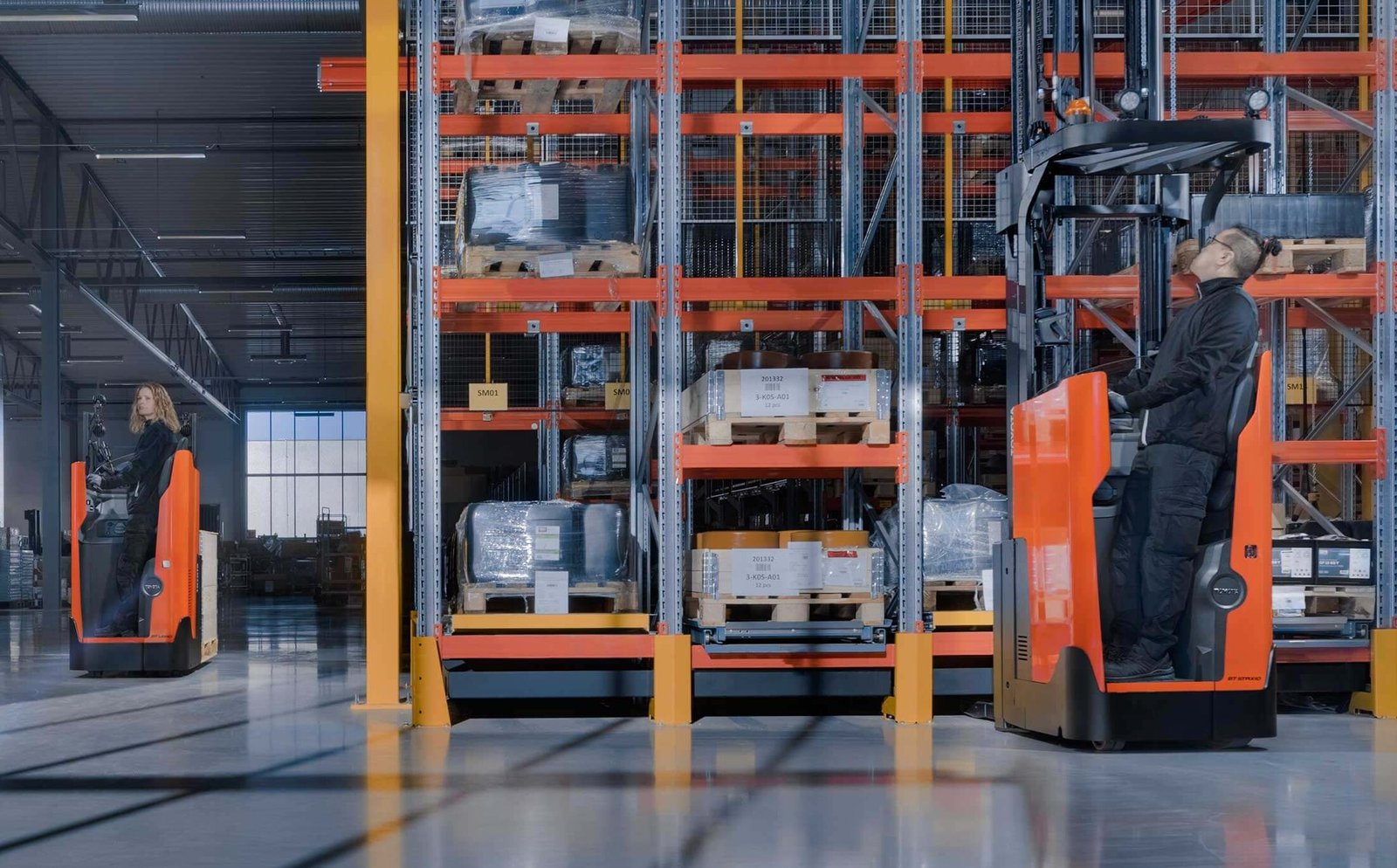
1. Lean Warehouse Operations and Practices
Implementing lean practices is crucial to reduce waste and enhance warehouse efficiency. Start with a well-thought-out warehouse layout to cut down on unnecessary movement, making it easier for employees to navigate and find items quickly.
2. Fast Shipping and Quick Turnarounds
Quick shipping is integral to maintaining a competitive supply chain. Organise your warehouse using clear labelling and designated sections. Batch and zone-picking methods can speed up fulfilment, while thorough training helps minimise errors.
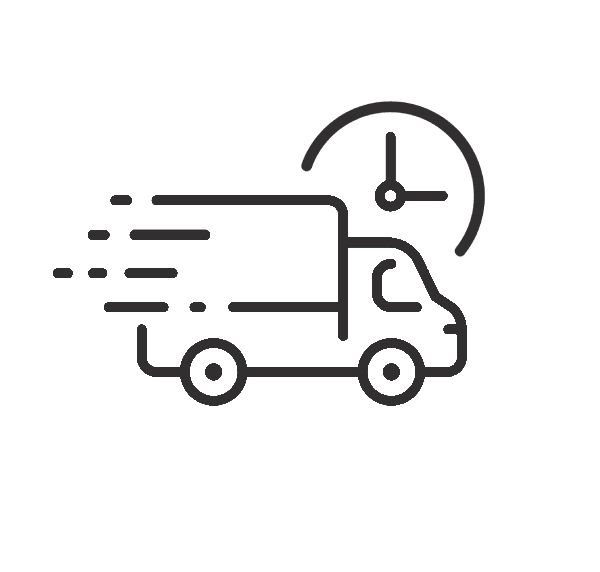
3. Create Thorough Employee Training Processes
Employees play a crucial role in warehouse efficiency. Developing robust training programs that cover inventory management, equipment handling, and safety protocols leads to higher productivity and fewer mistakes.
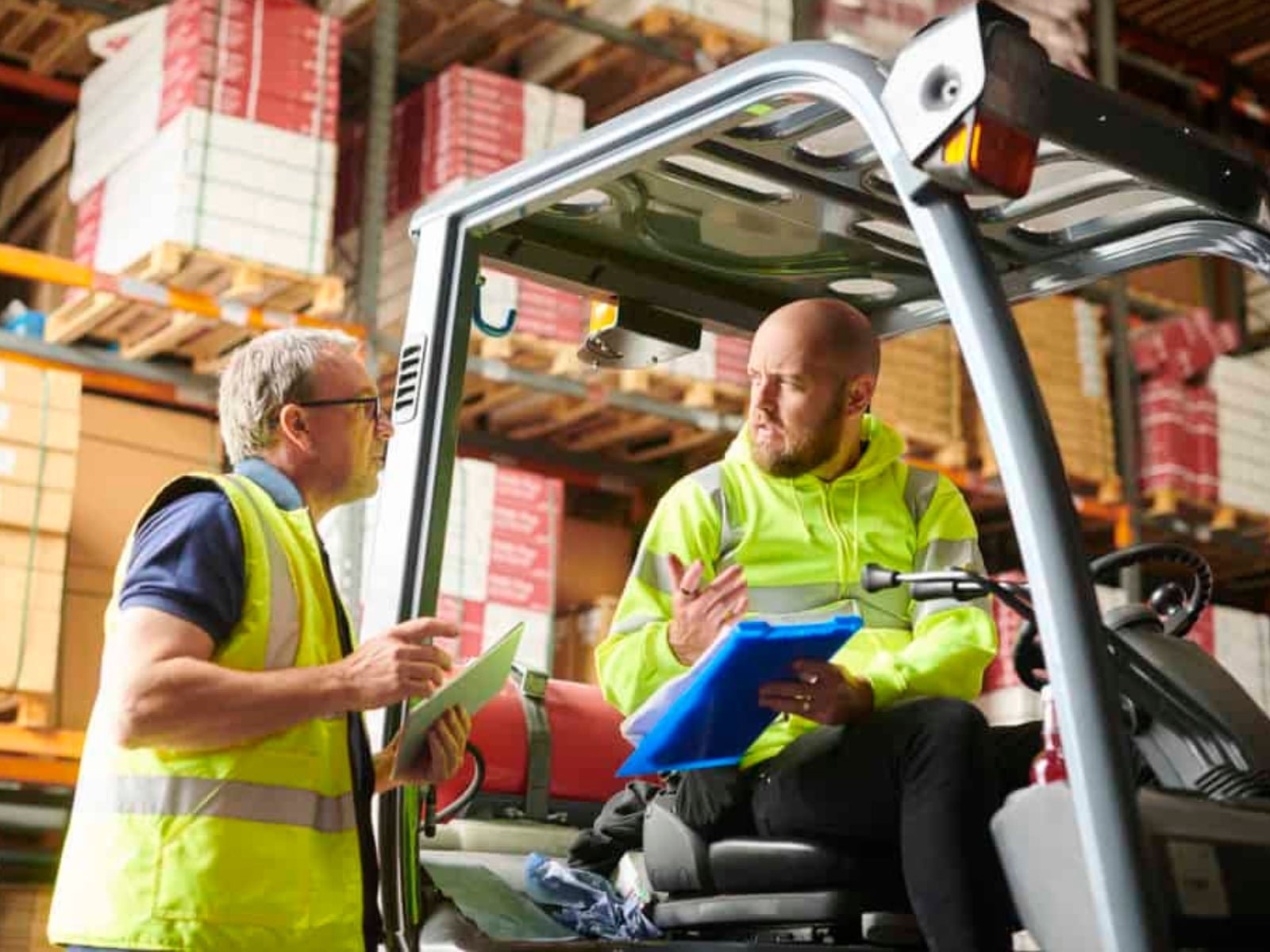
4. Offer Omnichannel Warehousing
Modern consumers expect seamless shopping across various platforms. Implementing omnichannel strategies can enhance warehouse efficiency by integrating inventory management and order processing across all channels.
5. Regularly Review Your Warehouse for Effectiveness
Routine reviews are essential for optimising warehouse efficiency. Regularly assess your warehouse layout, storage space usage, and order processing. Pinpointing inefficiencies and making necessary adjustments ensures you remain competitive and efficient.
6. Organise Your Inventory Efficiently
Effective inventory management is essential for enhancing warehouse productivity and ensuring smooth operations. Start by arranging products in a logical manner, placing fast-moving items near packing zones to minimise retrieval time and speed up fulfilment. Utilising warehouse management software allows for real-time tracking, reducing stock discrepancies and providing better oversight of your inventory. This can significantly improve order accuracy and streamline the picking process.
When combined with the efficiency of Toyota order pickers, your warehouse efficiency can improve even further. Low-Level Order Pickers (LLOP) are ideal for operations where items need to be picked from lower levels. These machines are known for their speed, agility, and various accessories that support the order-picking process. Features like operator platforms that can raise during operation make accessing items at lower levels simple and efficient, which is particularly useful in fast-paced e-commerce and retail warehouses.
For reaching items stored at greater heights—up to 12.1 metres—High-Level Order Pickers are indispensable. These forklifts are specifically designed for high storage retrieval and are a must-have in warehouses where vertical space is utilised with tall racks. Their design ensures safe and efficient picking, optimising space usage and contributing to quicker fulfilment times.
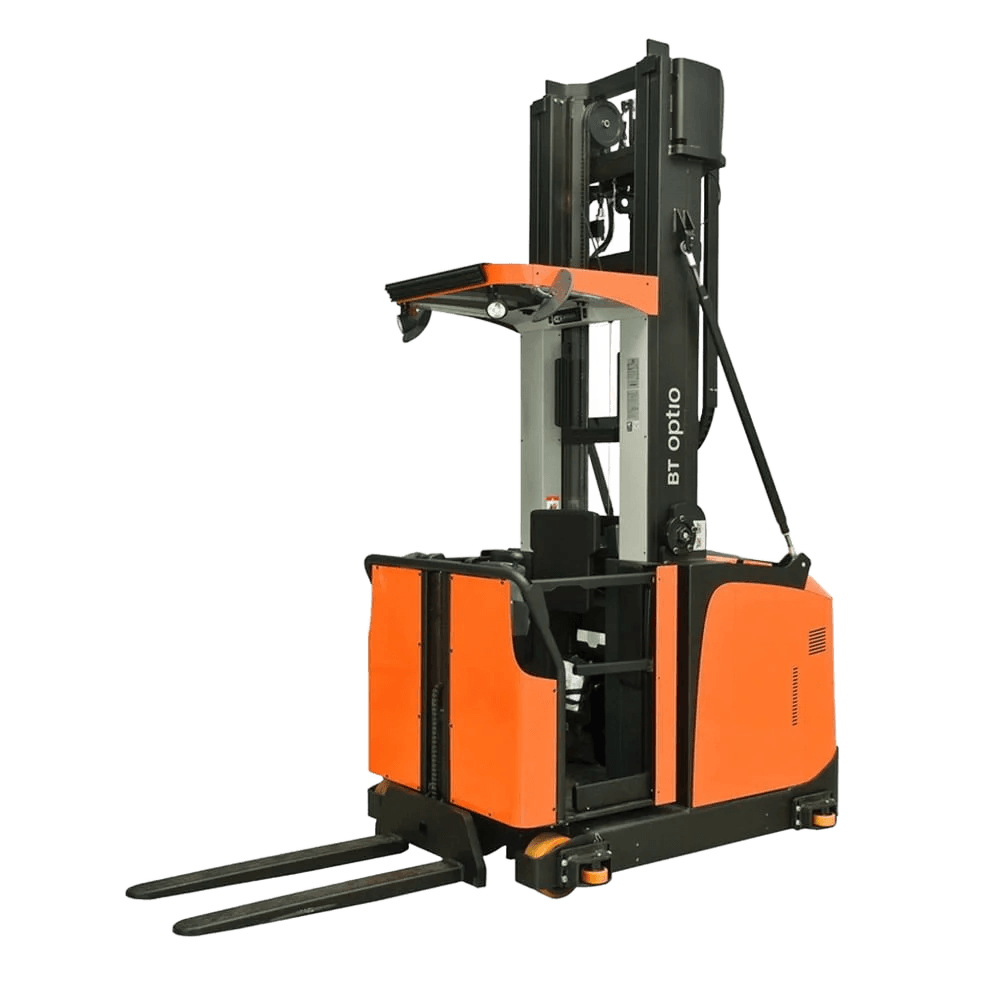
7. Run Regular Audits of Your Warehouse
Conducting audits is vital for spotting inefficiencies in your processes. Evaluate your warehouse layout, picking procedures, and employee performance to discover areas for improvement. Regular audits help you make informed decisions to optimise storage space and workflow.
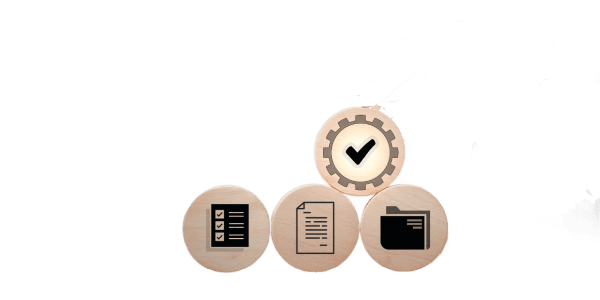
8. Implement the ABC Analysis Method
The ABC analysis method helps prioritise inventory management. This analysis can improve warehouse efficiency by allocating resources to high-priority items and ensuring frequently sold products are easily accessible.
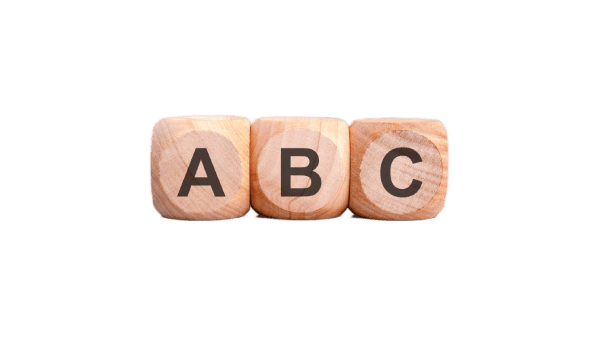
9. Improve Your Warehouse Picking Methods
Selecting the right picking method, such as zone picking or wave picking, can greatly impact your warehouse’s efficiency. Pair these methods with the ABC analysis to reduce travel time and streamline operations. This is one of the most practical warehouse efficiency tips to consider.
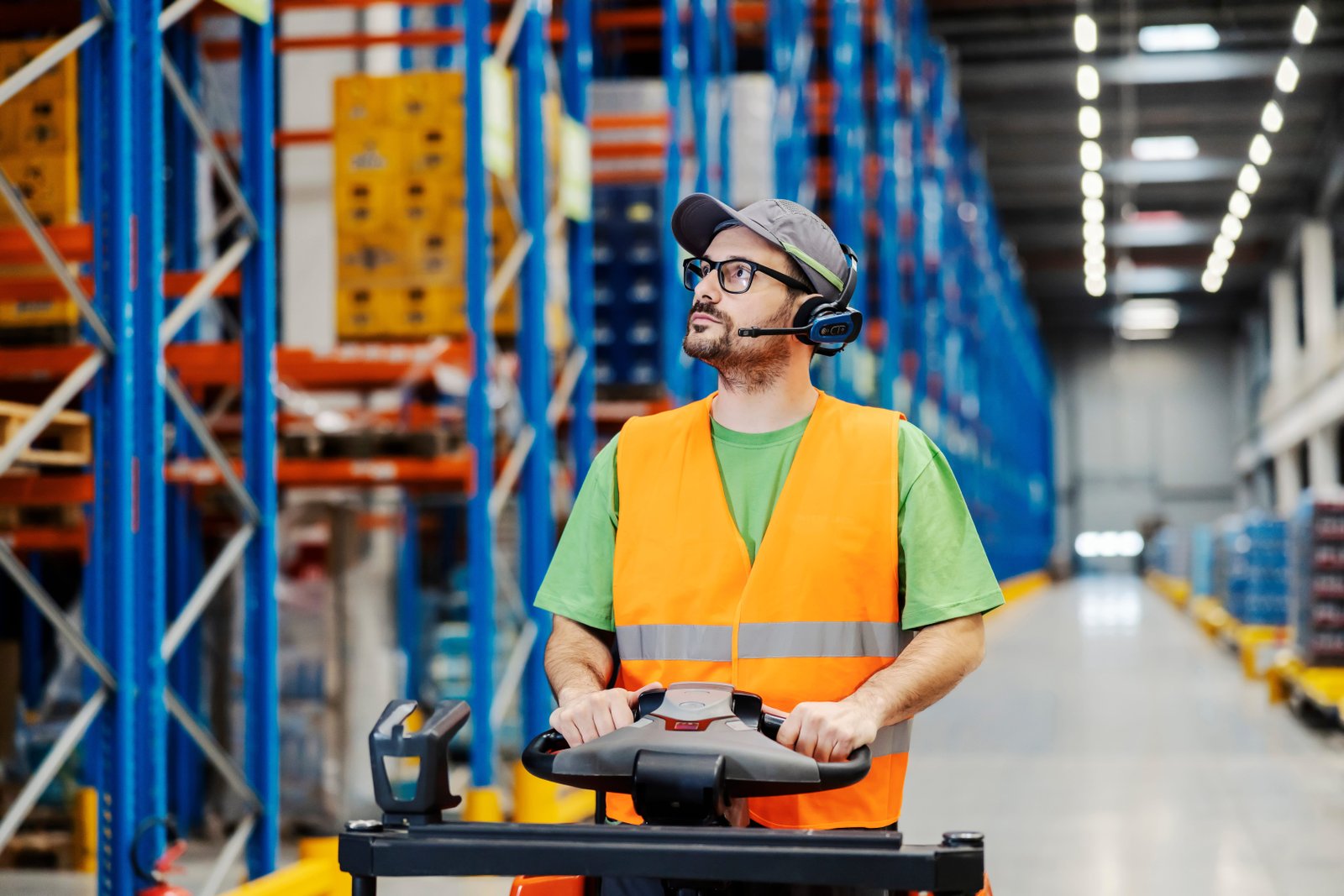
Request a Callback.
Please fill in the necessary details and we will respond to your enquiry as soon as possible.
10. Create Clear Communication With Your Employees
Strong communication is vital for maintaining warehouse efficiency. Establish clear guidelines and document procedures. Hold regular meetings and feedback sessions to ensure everyone understands their roles and responsibilities, boosting overall effectiveness.
11. Invest in High-Quality Equipment
Reliable, high-quality equipment is essential for maintaining efficient and productive warehouse operations. Easy Truck offers a wide range of material handling solutions that prioritise safety and boost productivity. By investing in Easy Truck’s equipment, you can experience significant improvements in both warehouse efficiency and space optimisation.
One standout solution is the Bendi forklift, which can transform how you manage your storage. This forklift can increase storage capacity by up to 50%, allowing you to use more of your warehouse space effectively. It operates in aisles as narrow as 1.6m, maximising storage density without sacrificing accessibility. With the ability to lift up to 13m, it helps you make better use of vertical space and reach higher storage racks. The Bendi forklift works seamlessly in both indoor and outdoor settings, offering flexibility for various warehouse environments. Additionally, it does not require aisle guidance or super-flat floors, simplifying infrastructure needs and reducing installation costs.
Beyond providing advanced equipment, Easy Truck supports your operations with an extensive maintenance fleet and comprehensive service packages. This ensures that your machinery stays in peak condition, minimising downtime and extending the lifespan of your investment. With Easy Truck, you can be confident that your equipment is well-maintained, allowing you to focus on maximising productivity and keeping your operations running smoothly.
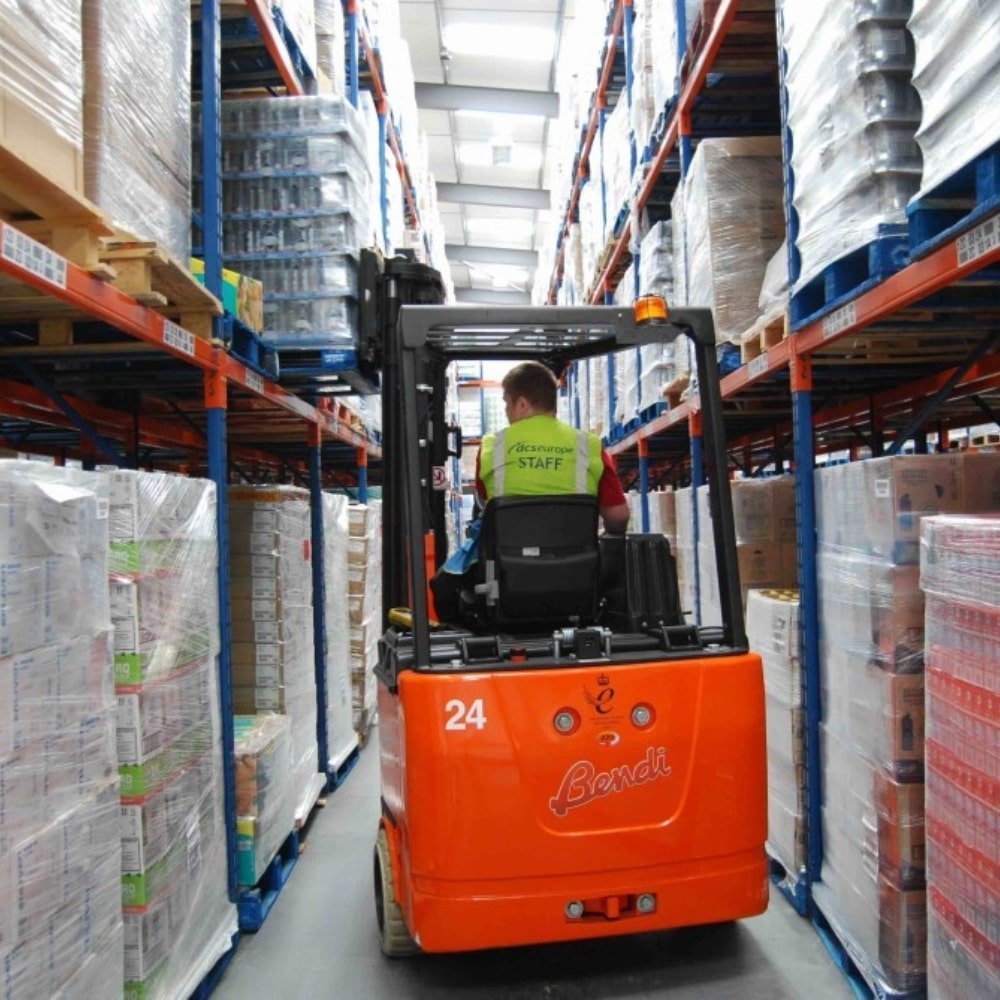
12. Take Advantage of Technology
Adopting advanced warehouse technology can significantly boost the efficiency and accuracy of operations. Tools such as barcode scanners and RFID systems enhance inventory management by reducing manual errors and accelerating processes. Integrating warehouse management software and pick-to-light systems into your workflow further optimises picking and fulfilment, streamlining the entire operation.
These technologies can be seamlessly paired with Easy Truck’s order picking equipment for even greater efficiency. For example, the optional powered E-bar allows for easy mounting of ancillary equipment, making it adaptable to various operational needs. Additionally, some order pickers come equipped with the “Smart Truck” system, featuring telematics hardware as standard. By connecting with I_Site from Toyota, these smart trucks provide valuable insights into battery management, geolocation, impact monitoring, and more. This data helps warehouse managers make informed decisions that enhance productivity, improve safety, and extend the lifespan of equipment.
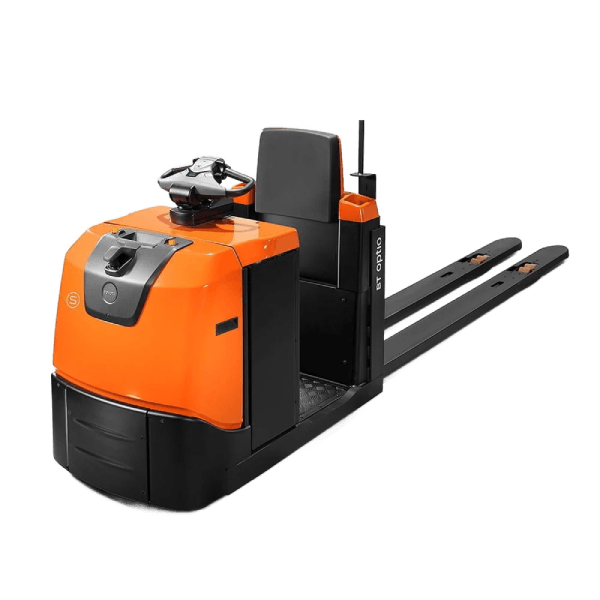
13. Invest in Reliable Equipment
Equipping your warehouse with reliable machinery is essential for maintaining smooth and efficient operations. Easy Truck’s range, which includes Toyota forklifts and Bendi Articulated Forklifts, is designed to support seamless workflows and meet the demands of various warehouse tasks. To keep your material handling equipment in top condition, Easy Truck offers comprehensive service options tailored to ensure operational continuity.
Our team of trained Field Service Engineers provides on-site forklift servicing for everything from routine maintenance to emergency breakdowns. We prioritise rapid attendance and strive for a first-time fix whenever possible, minimising disruption to your operations. Regular maintenance checks can also identify potential issues early, helping to prevent costly repairs down the line. Adjusting and lubricating parts prone to wear and tear extends the lifespan of forklifts and ultimately saves money by avoiding major breakdowns.
Easy Truck’s service vehicles are fully equipped and stocked with genuine OEM parts, allowing us to reduce equipment downtime as much as possible. This means your business can continue running smoothly, with minimal interruptions, and maintain optimal warehouse efficiency.
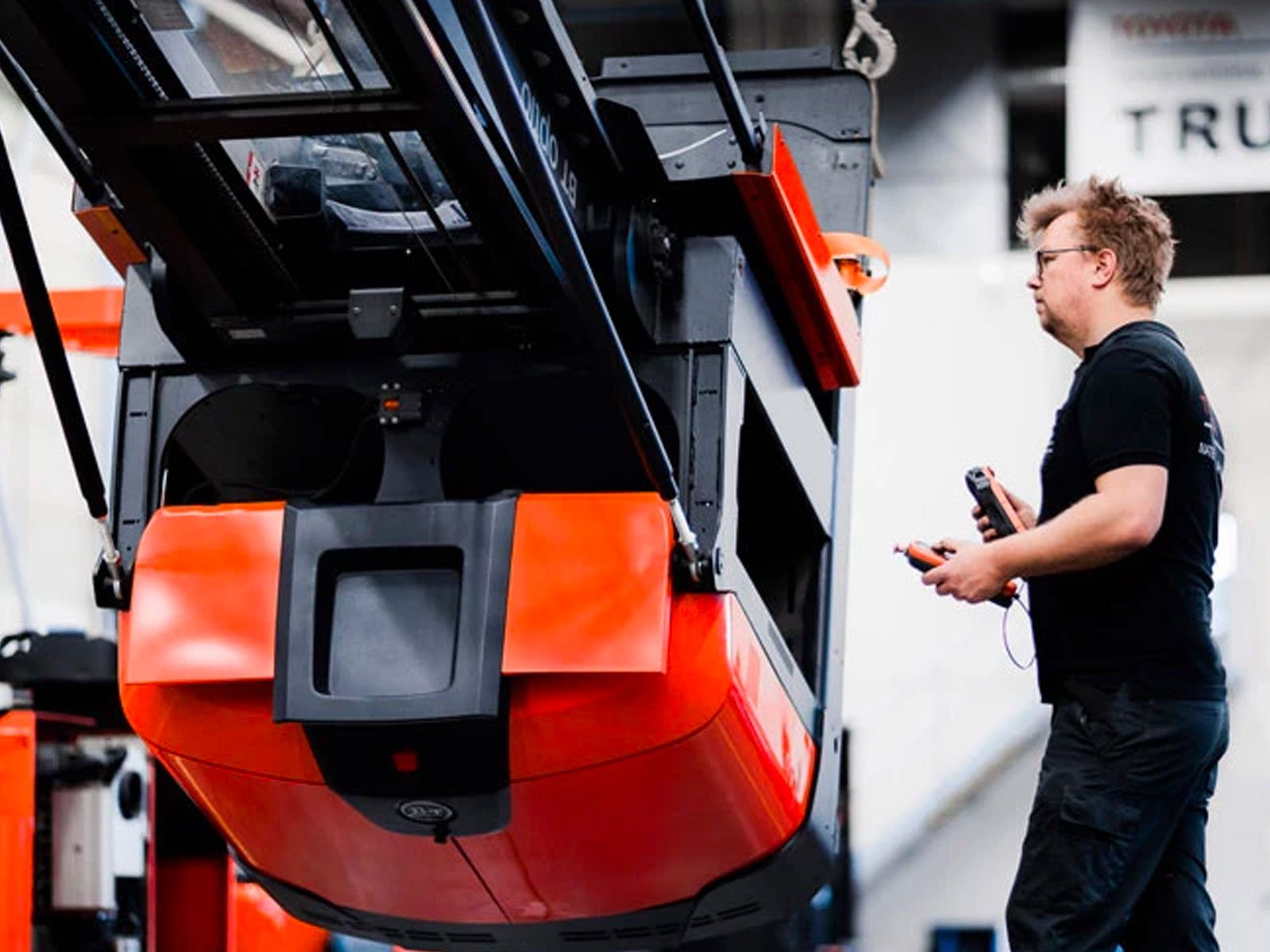
14. Get Employee Input
Employee feedback is invaluable for spotting inefficiencies that management might overlook. Regular input sessions help fine-tune your warehouse layout and processes, improving productivity and storage space usage.
15. Invest in Pick Assisting Technology
Integrating pick-assisting technology such as mobile barcode scanners and automated systems can greatly improve warehouse efficiency by minimising human error and accelerating order preparation. These tools allow employees to focus on more complex tasks that require human oversight, enhancing overall productivity and workflow.
According to an article by micronordic.com, there are several top-tier warehouse scanners to consider for optimising operations:
- Zebra MC9300: Known for its durability and reliability in demanding environments, making it an excellent choice for heavy-duty warehouse use.
- Honeywell Granit 1981i: A rugged scanner designed to withstand tough conditions, offering long-range scanning capabilities for enhanced flexibility.
- Zebra DS3678: This model is ideal for high-performance scanning and provides both wired and wireless functionality.
- Honeywell Dolphin CT60: Combines advanced scanning with mobile computing, supporting real-time data access and efficient task management.
- Zebra TC8300: Features an ergonomic design that reduces muscle fatigue and increases productivity by simplifying scanning tasks.
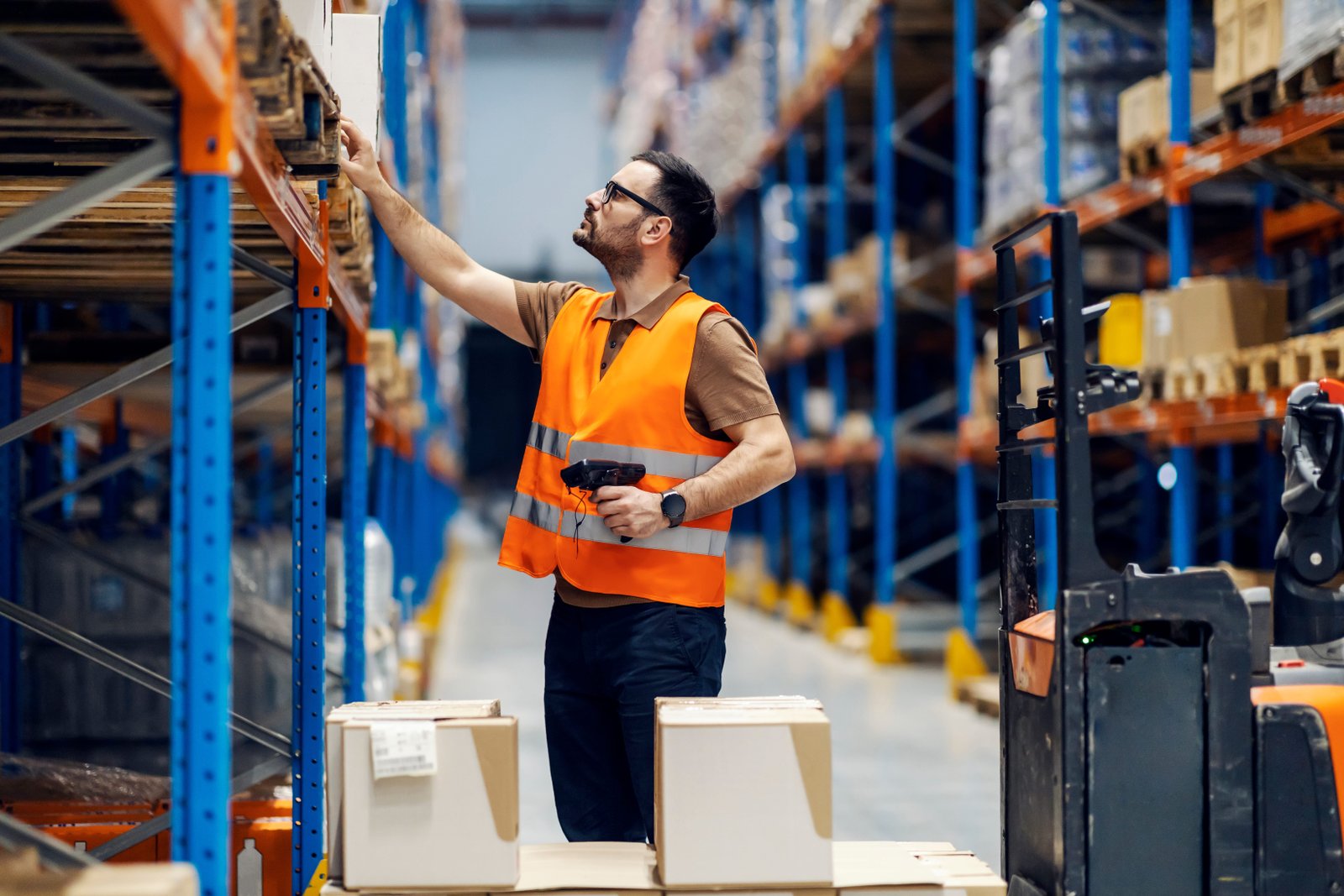
16. Reduce Travel Time
Optimise your warehouse layout to minimise employee travel time. Position high-demand items closer to packing stations and consider batch picking to reduce the number of trips needed. These simple changes can improve warehouse efficiency and cut down on labour costs.
17. Invest in a Quality Racking System
Maximising storage space with a well-planned racking system can greatly enhance your warehouse’s capabilities. Easy Truck’s warehouse racking solutions optimise both vertical and horizontal space, reducing travel time and enhancing workflow.
Easy Truck – Your Trusted Toyota Material Handling Dealer in the Midlands
As the official Toyota Material Handling Dealer for the Midlands, Easy Truck offers a full range of high-quality intralogistics solutions tailored to your specific needs. Whether you operate in manufacturing, warehousing, or production, Easy Truck can supply the perfect equipment to elevate your operations. Our product range includes:
- Counterbalance Forklifts – Available in gas, diesel, and electric models.
- Reach Trucks
- Powered Pallet Trucks
- Stackers
- Order Pickers
- Very Narrow Aisle (VNA) Machines
In addition, Bendi Articulated Forklifts provide unmatched versatility, combining the benefits of counterbalance, reach, and VNA trucks in one efficient machine. Bendi forklifts can:
- Increase storage capacity by up to 50%
- Operate in aisles as narrow as 1.6m
- Lift up to 13m
- Work both inside and outside without needing aisle guidance or special floor preparation
This versatility saves your warehouse space, time, and money. Whether you’re looking to buy outright, lease, or contract hire, our experienced team of specialists will work with you from consultation to equipment delivery to ensure a solution that’s perfectly suited to your needs.
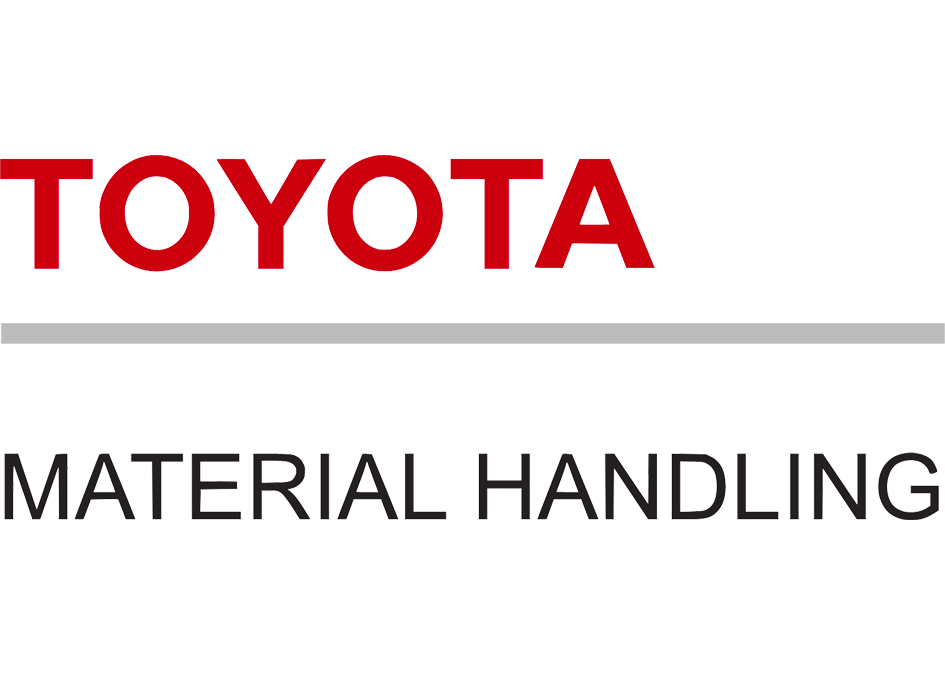
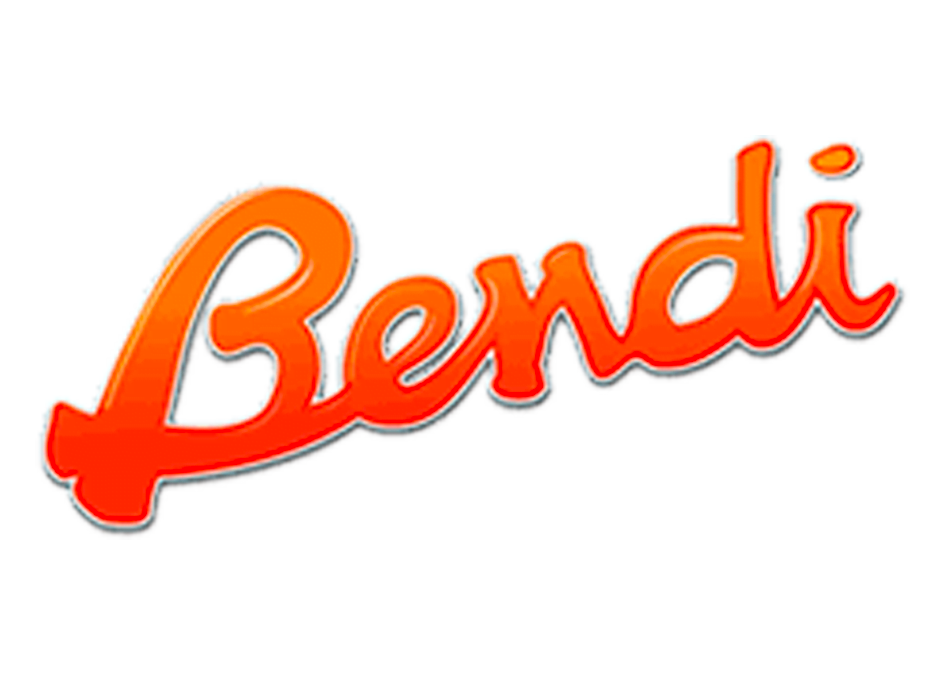
Improve Safety and Productivity with Tailored Cleaning Solutions
Maintaining a clean and safe working environment is key to improving warehouse safety and efficiency. Easy Truck provides tailored cleaning solutions that meet your specific needs. From industrial vacuum cleaners and pedestrian sweepers to scrubber driers and ride-on models, Easy Truck’s Kärcher range of cleaning equipment ensures a spotless and safe workplace.
By offering both new and refurbished options, Easy Truck helps businesses of all sizes find the right cleaning solution without straining their budget. Investing in the right cleaning equipment can help reduce accidents, increase productivity, and maintain a professional and organised warehouse environment.
Conclusion
By implementing these 17 tips, from lean operations and advanced technology to quality training, cleaning solutions, and high-end equipment, you can transform your warehouse into a top performer. Prioritise efficiency, stay open to employee feedback, and regularly review your processes to maintain a competitive edge. With the right strategies and support from Easy Truck’s comprehensive solutions, including Toyota forklifts, Bendi Articulated Forklifts, and tailored cleaning equipment, your warehouse can truly become No.1.